
CIMAC issues guidelines on used oil analysis for marine engines
In February 2023, Working Group 8: Marine Lubricants (WG8) of the International Council on Combustion Engines (CIMAC) published new guidelines on used engine oil analysis to promote the reliable operation of marine engines. CIMAC is a global non-profit association that advocates the importance of the internal combustion machinery industry and comprises national member associations and corporate members from 14 countries across America, Asia and Europe.
WG8 assembles a broad range of industry experts that includes ship operators, engine and equipment manufacturers, oil and additive suppliers, classification societies and scientific institutions. Chaired by Dorthe Jacobsen of MAN Energy Solutions, the working group plays a vital role in developing recommendations around marine lubrication and establishing common industry positions for the use and maintenance of lubricating oils.
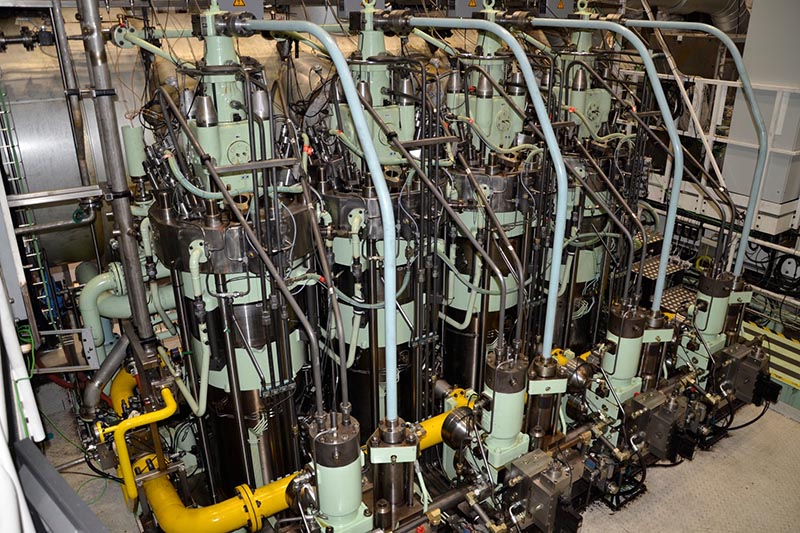
The 2023 CIMAC Guideline: Used Engine Oil Analysis builds on CIMAC’s existing body of knowledge relating to used engine oil and includes direct references to supplementary information.
Proactive maintenance is essential to identify signs of mechanical failure and used engine oil analysis plays a central role in diagnosing the health of an engine. The CIMAC guidelines emphasise the benefits in reducing equipment downtime, by allowing problems to be rectified before a breakdown occurs, and enabling longer equipment life through optimal lubrication and minimising wear. The analysis provides a breakdown of lubricant condition and suitability for further use while also offering potential cost savings by ensuring lubricants are not changed prematurely.
Arguably, the importance of used engine oil analysis is heightened in a marine environment—as ships navigate far out in the open sea. While relatively simple to perform, the complexity is in interpreting the results. CIMAC acknowledges that used oil analysis and monitoring has a wide variety of applications in the marine environment—however, the current recommendations are limited to used engine oil analysis only.
In its guidelines, the industry association reiterated the importance of ensuring a regular pattern of sampling to establish a credible historical trend of both machine and oil performance. Where possible, maintenance personnel should follow recommendations from OEMs or classification societies’ guidelines on sampling frequency. In the absence of such advice, CIMAC indicated analysis be completed every 1,000 to 2,000 hours in low-speed engine system oil, 500 to 1,000 hours in a medium-speed engine and every 250 to 500 hours in a high-speed engine. The guidelines also recommend low-speed engine scrape down oil, also known as drip oil, is analysed after reaching high load, after every fuel change and after changing oil feed rate settings. Scrape-down oil is collected from the scavenge space of marine two-stroke engine cylinder liners and can effectively track cylinder condition and identify remedial action when monitored regularly.
WG8 highlighted several key criteria to ensure a representative sample is captured including preliminary flush sampling, maintaining consistent intervals and the correct sample location. Sampling needs to be completed at operating temperatures with a fresh oil sample as a baseline. The working group also noted the influence of the quality and type of fuel burned and the performance of lubricating oil on used engine oil analysis.
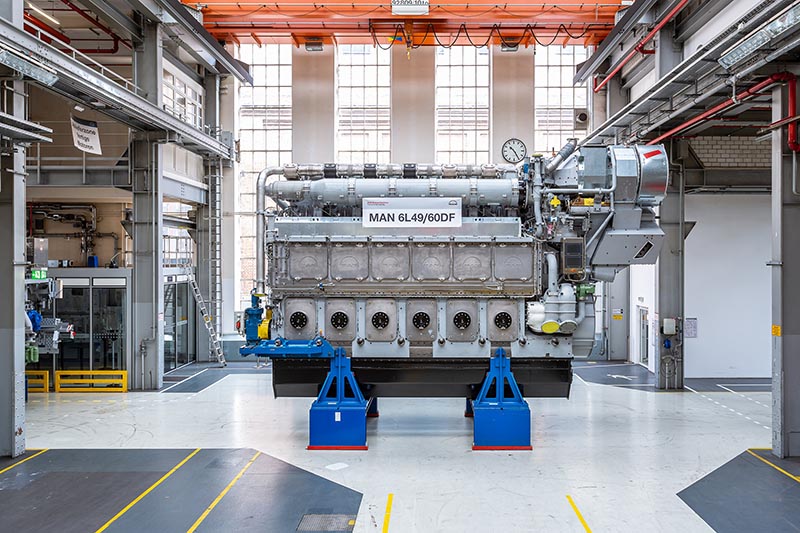
CIMAC provided detail on the parameters that should be assessed and the interpretation of results in both four-stroke and two-stroke marine engines.
Increases and decreases in viscosity and Basic Nitrogen (BN), decreases in flash points and an increase in water content and insolubles should be monitored in four-stroke engines. CIMAC outlined a variety of potential causes of an increase in viscosity including residual fuel ingress, asphaltenes,
oil ageing and oxidation, contamination, additive degradation, inadequate purifier operation, high soot, incorrect oil grade used and emulsion. These developments can contribute to higher temperatures and friction, deposits and lead to bearing damage. Decreases in viscosity can also increase the risk of bearing damage and can be onset by distillate fuel dilution, oil shear and incorrect oil grade usage.
The use of high BN oils can increase piston top land and exhaust valve deposit formation, whereas decreases in BN are attributed to the impacts of high sulphur fuel—which can trigger corrosion of cylinder components and deposit build-up.
Corrosion, bearing damage, sludge deposits and filter blockage are all potential risks of an increase in water content. The CIMAC paper lists cooling water leakage, condensation and incorrect purifier settings as underlying causes. Flash point decreases can be produced by distillate fuel dilution leading to a potential reduction in viscosity and bearing damage.
Residual fuel ingress, asphaltenes, oil ageing, contamination, wear debris, extended oil drain intervals and inadequate purifier operation are some of the potential reasons for an increase in insolubles which can increase the risk of friction, accelerated wear, filter blockage, deposits, the formation of sludge and bearing damage.
Changes in trends of these key parameters need to be investigated to mitigate risks and maintain the integrity of used oil analysis, says CIMAC. The guidelines also directed maintenance personnel to CIMAC Recommendation 29 and CIMAC Recommendation 20 for further information on analysis and interpretation in medium-speed and high-speed four-stroke engines.
Similar parameters require ongoing monitoring in used system oil analysis in two-stroke engines. WG8 noted the strong influence of lubricating oil treatment systems on lubricating oil suitability and performance and the detrimental impact that scrape down oil leakage through piston rod stuffing box, water contamination and contamination with fuel can have on system oil performance.
Viscosity increases in two-stroke system oil analysis can occur due to stuffing box leakage, oil oxidation, inadequate purifier operation, residual contamination and incorrect oil use and can lead to higher bearing friction and deposits. Similarly, viscosity decreases may be initiated by stuffing box leakage or distillate fuel contamination and have been associated with bearing failure.
Monitoring of BN fluctuations is also critical. Decreases in BN can encourage crankcase deposits and corrosion, whereas an increase in BN can impact water separation. CIMAC emphasised the importance of using the correct oil viscosity grade to alleviate potential nitrogen-related issues.
Contributing factors to an increase in water content in two-stroke engines include condensation, cooling water leakage, and inadequate purifier operation with a variety of knock-on impacts including corrosion, acid formation, reduced effectiveness of additives, hydraulic system failure and filter blockage.
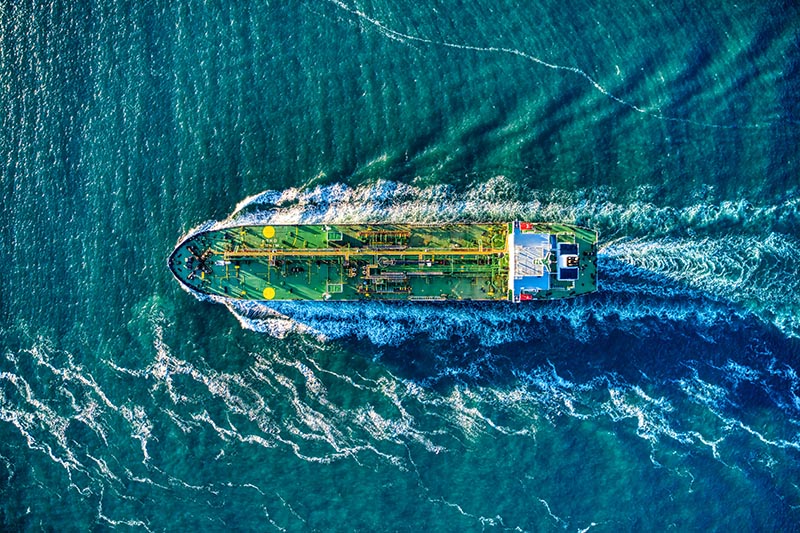
Finally, the paper reiterated the importance of tracking flash point decreases—which can be initiated by distillate fuel dilution from leaky fuel pumps—and an increase in insolubles, which have similar mitigating factors and outcomes as in four-stroke marine engines.
Sample composition in scrape down oil can vary significantly over time and from cylinder to cylinder, according to the CIMAC paper. A strong database of past samples is critical for meaningful comparison and accurate analysis and interpretation.
Scrape down oil analysis requires close attention to high or low BN, water content increases, presence of wear elements, such as iron, as well as chromium, molybdenum, copper, aluminium, silicon and vanadium. The presence of ferrous iron is a tell-tale sign of abrasive engine liner wear, whereas corrosive engine liner wear can be determined by the level of iron salts in samples.
The CIMAC guidelines contrasted shore laboratory-based analysis against shipboard methods. While laboratory methods involve sophisticated equipment and highly trained analysts, the document emphasised that ship operators must develop trust in shipboard analysis. It is a valuable tool to use alongside laboratory analysis with the advantage of rapid results that can be acted on immediately— and backed up with shore analysis.