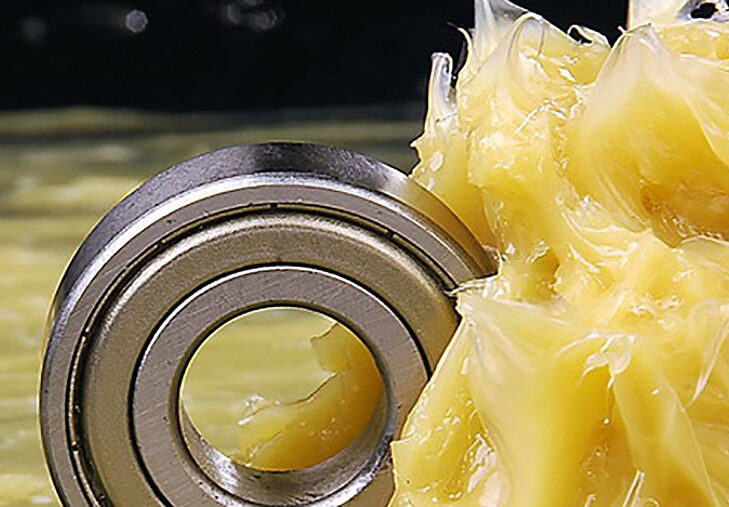
Electric vehicle greases – an unclear future
Automotive greases play a critical role in reducing vehicle friction and wear, protecting against corrosion, preventing contamination, water ingress and leakage. As early as 1400 BC, the Hittites, who occupied the ancient region of Anatolia (also known as Asia Minor, modern-day Turkey), used a blend of animal fats and limestone to lubricate axles and minimise wear on their chariots. Today, the global automotive grease market is expected to continue to rise at a considerable rate to 2026, according to recent research from Research Reports World. However, the emergence of electric mobility means the profile of the grease market is increasingly uncertain.
There are several possible pathways to vehicle electrification. As individual OEMs pursue multiple strategies, lubricant manufacturers must respond to these technical changes. Electric vehicle (EV) motors present different microenvironments to the ever-faithful internal combustion engine. “The performance requirements [of greases] will more than likely remain similar. It is the environments and the materials greases have to lubricate that will change,” says Ashlie Martini, professor of mechanical engineering at the University of California Merced (UCM).
Martini, who has been active in the area of tribology and lubrication engineering for almost two decades, is amid research on the “Tribological performance of market available electric motor greases and enhanced performance characteristics.” The project, supported by the National Lubricating Grease Institute (NLGI), examines the friction and wear characteristics of commercially available ISO 100 greases in conditions representative of EV motors.
EVs pose significant questions for lubrication engineers in the areas of noise reduction, energy efficiency, and the presence of electric currents and magnetic fields. Thermal transfer, seals and materials compatibility are also important considerations. “An umbrella product may not be sufficient for new challenges that arise for grease lubrication of electric motors in EV environments,” says Martini.
The absence of an internal combustion engine to mask vibrations, harshness, squeaks and rattles, heightens the importance of noise-reducing lubricants. Sound can also affect sensors that are integral to vehicle guidance and safety. Noise-reducing greases are different from those available on the market today.
Energy efficiency is directly related to lubricating film thickness. Thinner lubricants reduce viscous friction, allowing more energy to be conserved. However, greases can thin too much at high temperatures, thus “thinner lubricants bring their own challenges,” says Martini. A thinner film will be closer to the mixed and boundary lubrication regimes where wear is a concern. Striking a balance between the ability to remain in a full film lubrication regime, and the ongoing transition towards thinner lubricating films that enhance energy efficiency is both a “major hurdle as well as a major opportunity,” she says. The professor also emphasises the need for lower roughness surfaces to ensure a thin lubricating film can separate surfaces and mitigate wear.
At UCM, graduate student Daniel Sanchez Garrido characterises greases with similar International Standards Organization (ISO) viscosity grades, but different combinations of polyurea or lithium thickener with mineral or synthetic base oil. Though too early to make definitive statements, Sanchez Garrido says preliminary results indicate that each grease has its own performance trends in the simulated EV environment and different greases are preferred based on the test metric or test condition being evaluated.
Some market available greases are less adversely affected by higher temperatures and rougher surfaces, demonstrating a better ability to maintain full film lubrication under more severe operating conditions, says Martini.
Non-traditional materials used in EV components also present new unique challenges for lubrication engineers. Steel bearings are expected to be superseded by lighter weight, hybrid bearings that can mitigate issues with stray currents. The UCM researchers have observed diverse friction and wear behaviour using standard test protocol when replacing steel bearings with a ceramic alternative.
It is not just the demands of satisfying the new environments and materials associated with EV designs that are creating uncertainty for grease manufacturers. Insecurity around the shape of the grease market also includes instability of raw material supply. The most popular greases are lithium-based, with 72.26% market share according to the 2018 Grease Production Survey by the NLGI. Though, there are “indications that grease manufacturers are exploring other thickeners and emerging grease additives,” says Martini.

Lithium is becoming a mainstream chemical as the substance of choice in EV battery technology. The lithium market share for energy storage is 59% compared to 9% for lithium grease, creating a David vs Goliath-type situation. This imbalance leaves greases at a significant disadvantage and diversion of lithium supply to energy storage may intensify pressure on grease pricing. Earlier concerns around lithium scarcity may have eased, courtesy of an increase in production and greater efficiencies, though opinions are mixed on how the grease market will adapt in the shadow of EVs. Grease manufacturers may need to reconsider the role of lithium in grease.
The emergence of lithium recycling and a shift in lithium battery technology may provide light at the end of the tunnel. Lithium carbonate has traditionally been the compound-of-choice for producing lithium-ion batteries. Manufacturers are transitioning away from cobalt-rich cathodes toward nickel cathodes of which lithium hydroxide is the preferred precursor. Lithium hydroxide is the chemical of choice for greases. Some analysts believe this market swing will open more diversified supply for grease manufacturers.
EV technology is still evolving, so the industry and users will need to be flexible and ready to adapt to take advantage of “opportunities to explore emerging lubrication technology in the form of non-traditional thickeners and additives,” says Martini.