
Electric vehicles—rising costs, falling prices
The price of electric vehicles (EVs) will fall over the next 12 months as original equipment manufacturers (OEMs) compete to capture market share and race to reach economies of scale. This is a prediction in the latest Annual Battery Report produced by the Volta Foundation, a trade association dedicated to advancing the battery ecosystem.

The Volta Foundation’s report, published on January 15, 2023, summarises noteworthy developments in battery manufacturing over the past year and is compiled by crowd-sourcing information from industry and academia. Industry milestones, academic breakthroughs in battery science, new government regulations and short-term trends are outlined in the report.
EVs continued to rise in popularity in 2022, accounting for an estimated 10-13% of new car sales, with the penetration expected to continue to accelerate over the coming years. China delivered 50% of global EV sales and continues to lead the pack with around six million EVs on the road. The report identified China’s BYD as the leading manufacturer with a market share of 17%, which includes battery electric vehicles (BEV) and plug-in hybrid electric vehicles (PHEV). Tesla still leads for pure EV sales.
Volta Foundation highlighted projections from Boston Consulting Group (BCG) that 20% of light vehicles sold globally will be electric in 2025, and 59% in 2035. A year earlier, these projections were 11% and 45%, respectively.
Investments in EVs continue to accelerate. The key areas of focus for large automotive OEMs are charging infrastructure, critical mineral supply for batteries and vehicle manufacturing. Legacy automakers are becoming increasingly ambitious and scaling up EV manufacturing.
The global battery industry continues to hasten alongside EV growth. Despite macroeconomic headwinds, the battery report outlined a year-on-year increase in total investment from USD33 billion in 2021 to USD39 billion in 2022. A theme of increasing local and regional battery manufacturing is apparent with policymakers shifting their attention towards nationalisation effects, including in the United States.
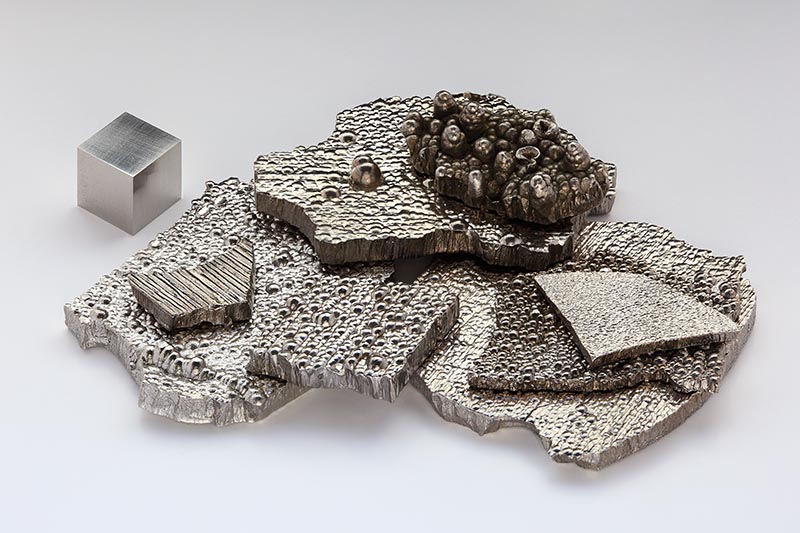
Production capacity expanded to approximately 600-700 gigawatt hours (GWh) in 2022 to meet growing demand (approximately 450 GWh) from automakers and other segments such as energy storage.
Greater adoption of EVs will continue to drive demand for battery raw materials and manufacturing capacity. Despite a prediction of falling EV prices over the next calendar year, in 2022, battery prices increased for the first time in 20 years. In its annual price survey, BNEF reported a 7% year-on-year increase to USD151 per kilowatt hour (kWh) with prices expected to remain steady in 2023. EV prices continue to be higher than the average vehicle, excluding in China, and recent developments have pushed out cost parity with internal combustion engine (ICE) vehicles to 2026 from 2024, according to the report.
The battery application, region and chemistry all impact battery prices. At USD138/kWh, passenger BEV battery prices are lower than stationary storage (USD169/kWh) and PHEVs (USD345/kWh). In Europe, average prices are USD169/kWh, versus USD157/kWh in Europe. China has the lowest price at USD127/kWh. The report also noted that lithium iron phosphate (LFP) cells were 20% cheaper than lithium nickel manganese cobalt (NMC) cells.
Raw material prices are rising throughout the entire value chain. Volta Foundation outlined sky-high prices for lithium, cobalt, nickel and electrolytes due to supply constraints, inflation, persistent covid-19 supply chain issues and geopolitical conflict.
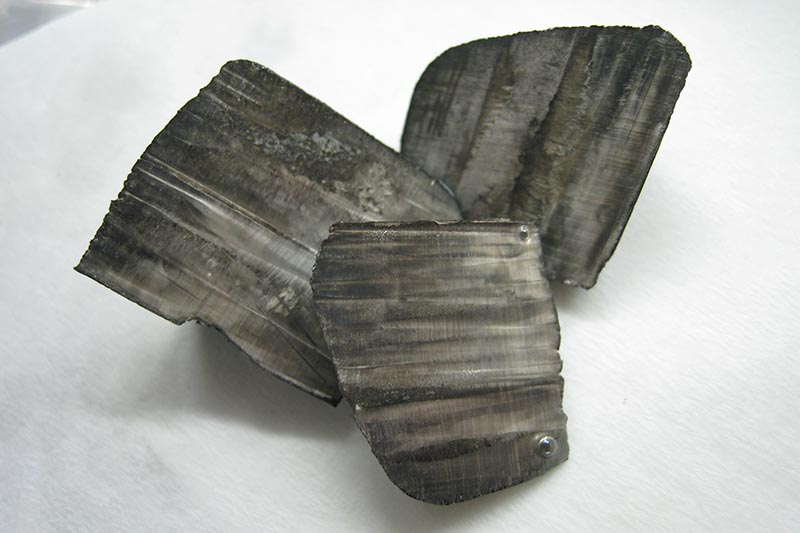
The report summarised significant raw material price fluctuations, particularly since mid-2022. A doubling in the price of nickel and cobalt and a four to eight times lithium hydroxide price increase led to an almost tripling in the cost of NMC materials in the past 18 months. LFP variants were impacted by a six to eight times rise in lithium carbonate prices compared to 2020-2021. Aluminium and copper prices also increased by greater than 50%. The trade association expects the cost of battery raw materials to continue to increase as supply chain capacity lags increasing demand—with a projected 10% increase in cathode active materials prices for NCM cathodes in 2023. The report also highlighted the difficulties rising prices pose for new market entrants without established long-term contracts.
However, a decline in battery pack prices is anticipated in 2024 due to falling commodity prices, new cell chemistries that use more nickel and less cobalt, LFP becoming more prominent and greater economies of scale. Cathode optimisation and other enabling technologies are an ongoing focus for commercial and entrepreneurial efforts.
Volta Foundation’s report referenced a recent white paper on the potential role of smaller battery packs as a solution to materials supply and cost issues—with the added benefit of lower emissions. The paper, published by Exawatt and Minviro, emphasised that 99% of UK car journeys are under 100 miles. Nevertheless, OEMs have maintained a greater focus on the luxury segment, including larger and more expensive SUVs, trucks and crossovers, and battery pack sizes are steadily increasing.
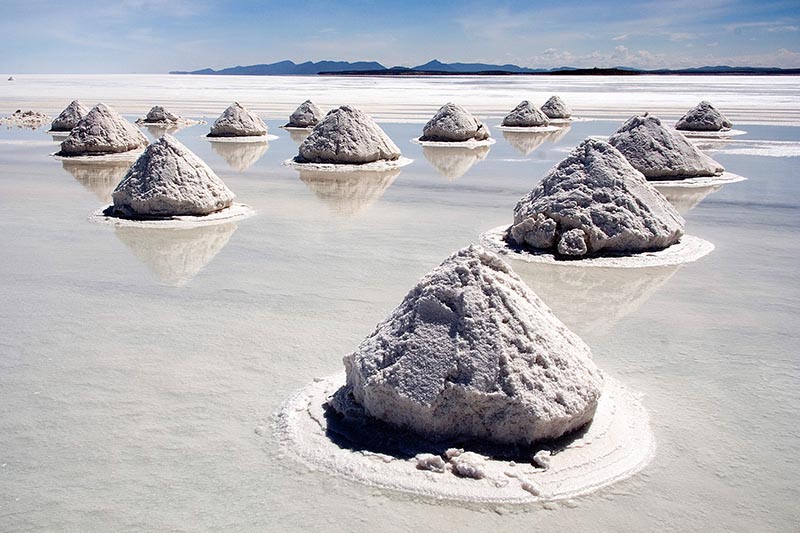
Australia, Indonesia and The Democratic Republic of Congo dominate the mining of battery raw materials. However, China remains the major player in the downstream supply chain and currently provides 75% of all battery cell manufacturing capacity, 90% of anode and electrolyte production, 60% of global battery grade lithium refining capacity and has increased its investments in carbonate and hydroxide refinery facilities. Most European countries declined in overall performance compared to the 2021 battery report. Volta Foundation expects lithium supply for EV batteries to remain tight throughout the current decade—unless new projects ramp up quickly—based on current EV sales forecasts and battery trends.
The scale-up of manufacturing is expected to encounter “growing pains” which the trade association says will be complicated by shortages in equipment, raw materials, personnel and manufacturing know-how. Challenges in the scale-up of pilot and gigafactories in the U.S. and Europe are expected.
There is significant variability in manufacturing capacity forecasts due to uncertain demand, raw materials and plant completion. Several European projects have already been paused or cancelled due to market conditions, such as the Northvolt and Varta, and the association anticipates further production delays will be announced in 2023. Assistance from other countries will be required to advance the U.S. manufacturing and battery supply chain, according to the battery report.
Changes to battery packs were outlined including a shift towards monolithic designs intended to eliminate dead weight and enable higher packing efficiency. The report predicted that cell-to-module and cell-to-pack designs will reach maturity and be commercialised in serial production cars in the next 12 months. This approach offers several advantages including fewer components, a decrease in battery assembly costs and a reduction in carbon intensity. Still, engineering challenges need to be overcome such as safety and thermal propagation.