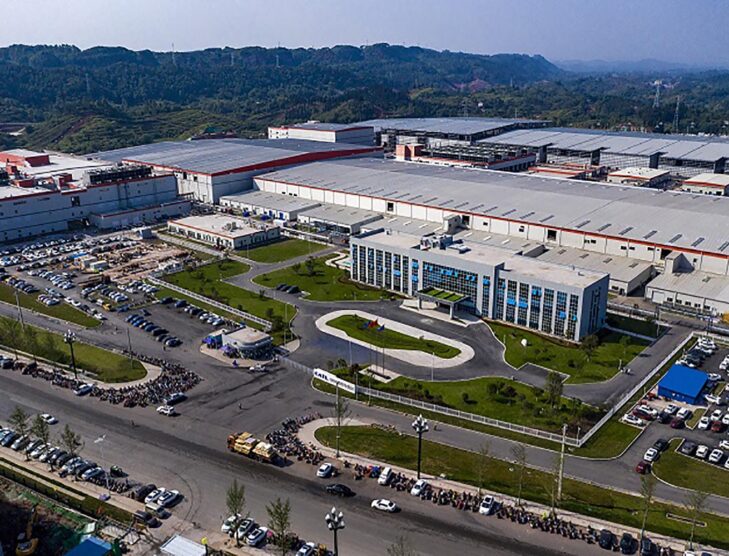
Greater regionalisation of battery supply chains seen
When it comes to battery manufacturing, Asia is the global kingpin and does not look like being dethroned any time soon. In 2020, Asia accounted for 85% of global lithium-ion battery manufacturing capacity, according to a report by Statista, a leading provider of market and consumer data. Japan and South Korea are prominent battery manufacturing countries. In fact, according to an analysis by VC Elements, the top 10 battery manufacturers in the world consist of only Asian companies.
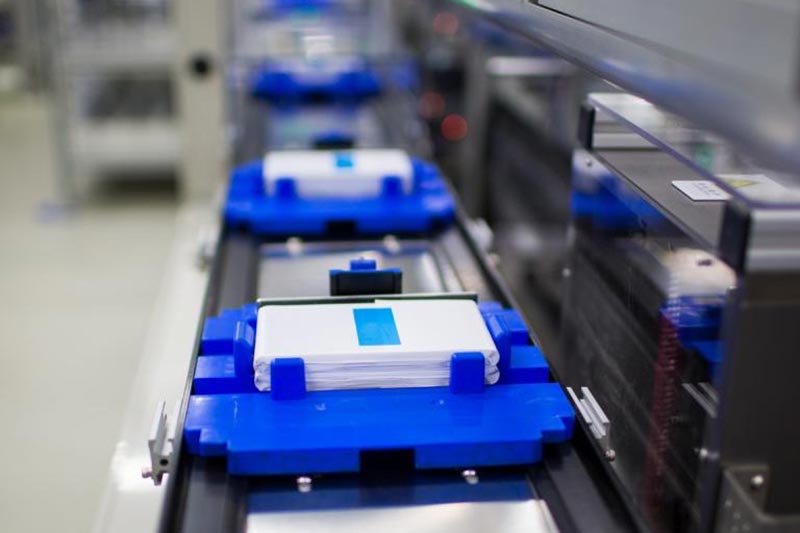
If you peek beneath the covers, it’s really all about China. China produced 77% of lithium-ion capacity in 2020. Europe and the United States contributed a paltry 6% and 9% respectively. This probably comes as no surprise, China is the largest market for electric vehicles in the world and has mandated that its car manufacturers use locally-built batteries in electric cars.
Very few automakers have ventured into manufacturing their own batteries for electric vehicles, with most racing to establish lithium-ion supply deals. China’s BYD is one OEM that is prospering in battery manufacturing, with an estimated 7% share of the battery market. However, there is a significant cost to becoming involved in battery manufacturing, meaning most automakers remain reliant on established manufacturers. This means reliant on China.
If there is one thing that the Covid-19 pandemic has taught us, it is the risk of overreliance on one country or supplier. The Covid-19-induced semiconductor chip shortage halted assembly lines around the world with some estimates suggesting it will cost the global automotive industry USD210 billion in revenue in 2021. Supply bottlenecks and risk mitigation have prompted Europe and the United States to consider greater localisation of battery manufacturing supply chains.
There are significant benefits to be achieved by regionalising supply chains: a reduction in shipping costs—which have skyrocketed during the pandemic, shorter lead times, cost reductions, local job creation and minimisation of political risk. Construction of battery ‘gigafactories’ in the West are a key component of regionalisation plans.
Europe and the United States have been criticised in the past for doing little to prioritise investment in the sector. Europe, in particular, has upped its game in recent years as it looks to reduce reliance on other regions for battery cell imports—not only for an electric vehicle future but also for the stabilisation of power grids. Germany is leading the way in Europe. In March 2021, Volkswagen announced plans to build six electric battery and electric vehicle component factories in Europe before the end of the decade. Estimates from Transport & Environment, Europe’s leading clean transport campaign group, indicate that at least 38 gigafactories are planned or under construction in the European Union and the United Kingdom. There have also been positive developments in the supply of sustainable raw materials.

Statista’s figures suggest that Europe is making progress. The company forecasts that the European share of global lithium-ion battery manufacturing capacity will reach 25% by 2025, the second-largest producer of lithium-ion batteries by some margin. Meanwhile, China’s share falls to 65%. Asia, excluding China, drops from 8% to 3% in the five years. The outlook is equally poor for the United States with its share expected to decline from 9% in 2020 to 6% in 2025.
However, recent analysis by CIC energiGUNE, the research centre of electrochemical and thermal energy storage and a strategic initiative of the Basque Government, indicates that interest is awakening among large automobile OEMs in the U.S., the engine room of the North American market. The company detailed several moves aimed at strengthening and regionalising supply chains.
General Motors has the most extensive portfolio of planned projects with plans to develop four factories in a joint venture with South Korea’s LG Energy Solutions. The Lordstown plant in Ohio will have a capacity of 35 GWh with production scheduled to commence in August 2022. A Spring Hill, Tennessee, plant operation with equivalent capacity will start production at the end of 2023. Ford Motor Company is collaborating with another South Korean company, SK Innovation, on three major projects to be launched between 2025 and 2026 in Kentucky, including two gigafactories with a production capacity of 43 GWh each.
While the gap between Europe and China may be narrowing, efforts to overcome China’s dominance could in the end be fruitless. A May 2020 review by Benchmark Mineral Intelligence suggested that 101 of the 136 lithium-ion battery plants in the pipeline to 2029 are based in China. Equally importantly, China controls the processing of most of the critical raw materials such as lithium, cobalt and graphite.
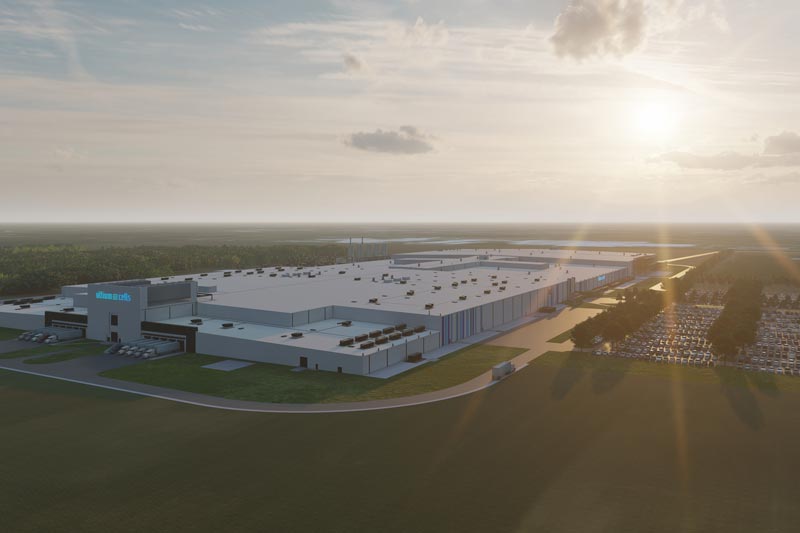
Many of the European investments do not cover the entire battery chain, just the battery cell manufacturing and there have been calls for greater investment in the mining of raw materials and the cathode, anode and precursor stages.
The reality is that some geographies are more abundant in raw materials. Chile, Australia, Argentina and China boast the world’s highest lithium reserves. Despite being ranked only fourth in terms of reserves, China controls the lion’s share thanks to its investments in Australia and South America. Chinese companies also control around 80% of the world’s cobalt capacity. For Europe, raw material supply and refining is a weak spot.
While Europe, and to a lesser extent America, are looking to regionalise their battery supply chains, the same cannot necessarily be said for Asia. With an expectation that most electric vehicles will be built near where they are used, Asian firms are beginning an assault on Europe. Many leading Asian battery manufacturers are expanding production capacity in Europe to maintain their supremacy. Europe is increasing local battery manufacturing capacity, but whether manufacturing plants will be owned by European or Asian companies is a bigger unknown.
Investment in battery manufacturing in Europe is higher than in China at present. However, new projects continue to pop up in the world’s most populous nation as it extends its arsenal of battery manufacturers. It is difficult to see China being overtaken in the short- to medium-term, particularly after the leg up local companies have been afforded by generous government subsidies over the past few years. Some analysts have compared battery manufacturing to the solar PV industry. Solar PV production started in Europe off the back of strong subsidies, only to be dominated by China owing to a faster ramp up and the dramatically larger scale of PV plants constructed in the region. Now eight out of 10 solar panels are made outside of Europe.
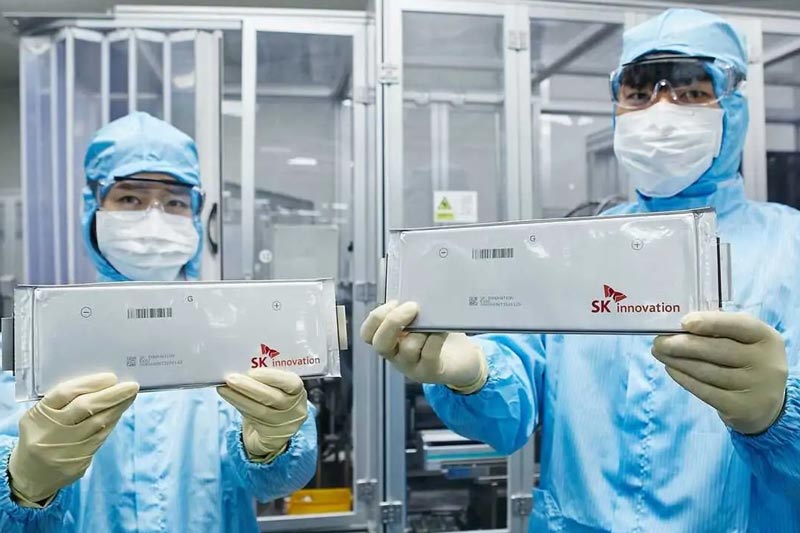
China’s Contemporary Amperex Technology Co, (CATL) broke ground on its first battery production site in Europe in Germany in October 2019 and, according to the company website, the development is making steady progress in 2021. Reports earlier this year indicated that BYD is also preparing its first battery factory in Europe and is currently recruiting engineers. In November 2020, China’s SVOLT announced plans to invest EUR2 billion (USD2.4 billion) in its first factory in Europe, in Germany. The company expects production at the Saarlouis site to commence at the end of 2023.
While the Asian expansion might be nerve-wracking for some European companies, not everyone is intertwining EV success with control of the battery market. Regionalisation is important to ease logistical and transportation concerns, but some analysts believe performance, price and availability are more important than whether the factory has national heritage. The choice of multiple specialist suppliers may enable success in the EV game.
Asia seems to be the clear winner in battery manufacturing. On the other hand, there have been suggestions that Europe and North America could hold an advantage when it comes to fuel cell manufacturing. Fuel cells are a comparatively small market, estimated at approximately 13,000 units in 2020, and are projected to reach 932,000 units by 2028 at a compound annual growth rate of 69.7%.
In July 2021, Europe unveiled plans to become the world’s hydrogen leader with a significant push to green hydrogen. In a speech at the European Hydrogen Week on November 29, 2021, Frans Timmermans, executive vice-president of the European Commission, confirmed he wanted the EU to take a clear lead in establishing a framework for a global hydrogen economy. The region invested in new generation electrolysers before the rest of the world and is the global leader in patents and publications on this technology. European countries are looking to expand the use of hydrogen. Pure-play fuel cell companies are also taking several steps to grow. However, Europe’s fuel cell market remains fragmented at this stage.
Hyundai and Toyota accounted for more than 90% of FCEV sales in the first half of 2021. In October 2021, Hyundai Mobis announced an investment of US 1.1 billion in two new hydrogen fuel cell plants in South Korea to “accelerate the hydrogen economy and to secure broader global market dominance.” Hyundai Mobis, Hyundai’s parts and service subsidiary, already has the largest fuel cell production capacity in the world.