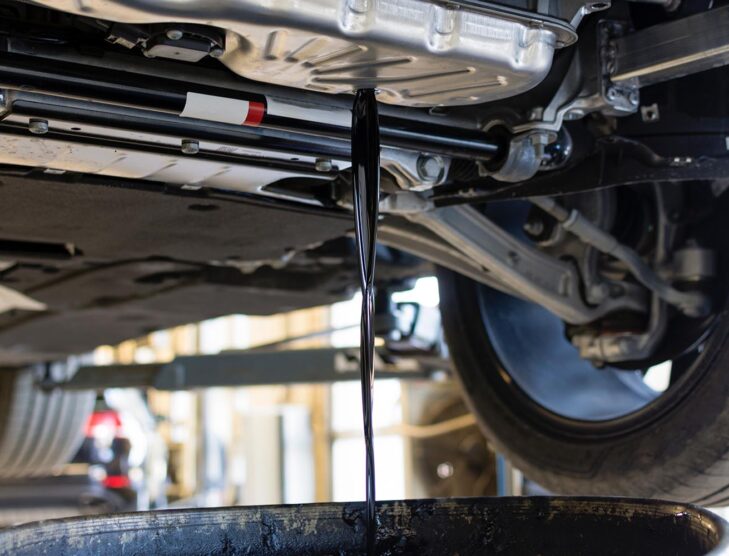
India’s shift to sustainable RRBO: Challenges and prospects
Processing of used oil falls into three basic categories. Recycled fuel oil (RFO) involves the filtering of oils to remove solids and low-temperature atmospheric distillation to produce a saleable heavy fuel. Vacuum gas oil (VGO) production requires an additional vacuum distillation step to yield a range of distillates. To manufacture re-refined base oil (RRBO) further solvent extraction or hydrotreating is completed to remove aromatics, improve colour and stability.
Of the 40 million tonnes of lubricants consumed globally, less than 10% of the blendstocks are RRBO, according to market research firm Kline & Company. However, interest in RRBO is expanding. By closing the loop of an industrial process, RRBO contributes to a circular economy and minimises oil disposal issues.
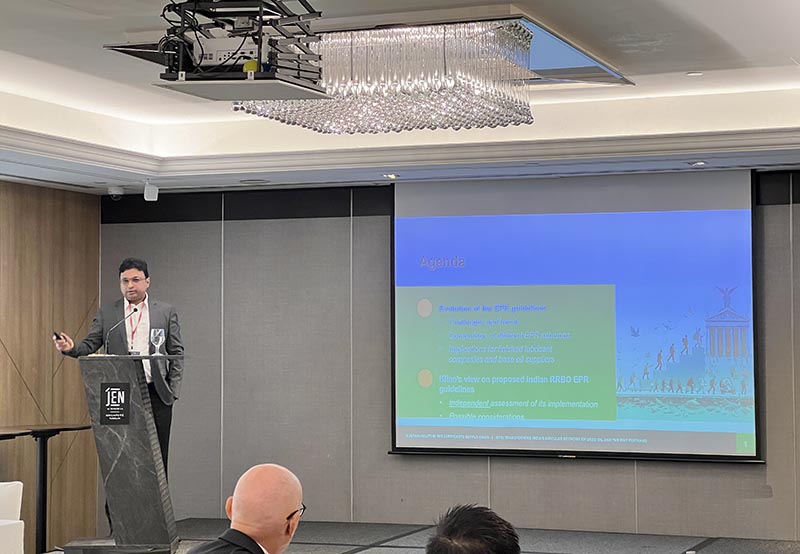
During the recently completed ALIA Seminar on Sustainability in the Lubricants Supply Chain, held at the Jen Singapore Tanglin by Shangri-La, Singapore on November 6-7, 2023, Raj Padmanabhan, Asia-Pacific regional product line manager at Chevron Oronite Pte Ltd., provided a snapshot of the RRBO market.
RRBO is now available from multiple producers globally with Group I, II and III in North America and Europe and Group I and II in Asia. The regenerated oils are utilised in additives and lubricants for the automotive, industrial and marine sectors. Some original equipment manufacturers (OEMs) are beginning to insist on minimum RRBO content in lubricant products, says Padmanabhan. Asia Pacific is the largest producer of RRBO, led by China’s capacity of 13.63 million metric tons, although the actual volume in circulation in the Chinese market is significantly lower, says Padmanabhan.
Padmanabhan also outlined a hypothetical comparison of RRBO and conventional base oils in finished oils. RRBO demonstrated a 50% to 80% reduction in the product carbon footprint (PCF). However, the Chevron Oronite representative acknowledged literature discrepancies regarding RRBO PCFs and the need to align on PCF methodology and calculations.

Several obstacles have impeded the growth of the re-refining industry including low rates of used oil collection, competition with the fuel market, inconsistent quality and supply, a fragmented industry and high rates of oil burning—all of which have meant major lubricant marketers have been reluctant to embrace RRBO.
Public policy on the “lubricants loop” is evolving, says Satyan Gupta, director, Energy Team at Kline & Company. In the past, policy has focused principally on collection to reduce the illegal discharge of used oil into the environment, with limited incentives for regeneration. Policies did not encourage circularity, says Gupta. The focus is shifting to encourage greater supply and the blending of RRBOs. In a presentation on the Evolution of EPR Guidelines for RRBO and Implications for Lubricant Marketers, Gupta signalled that the new norm in public policy is to focus on “RRBO quotas.” Several countries are introducing Extended Producer Responsibility (EPR) schemes for waste oil.
An EPR scheme extends a producer’s responsibility to the post-consumer stage of a product’s lifecycle, to ensure the circularity of their products. They are typically administered by a government or industry consortium and comprise regulations, policies and sometimes incentives. There is no common EPR model on how to address circularity, says Gupta, although they typically incorporate a combination of four principles—bans on the burning of used oil, incentivising the collection and the regeneration of used oils to produce RRBO, and mandatory quotas on RRBO content in lubricant sales.
Turkey and India have both introduced mandates. In December 2020, Turkey enacted regulation related to the management of used oils, including a progressively increasing target on RRBO content in finished lubricants—starting at 8% in 2024.
In May 2023, India published a draft notification of proposed RRBO EPR guidelines. The initial target of 10% has now been reduced to 5% RRBO content in finished lubricants from April 1, 2024. This requirement is set to increase annually. The original target of 60% by 2029 has now been reduced to 50%. Other jurisdictions are mulling regulatory changes more focused on regeneration.
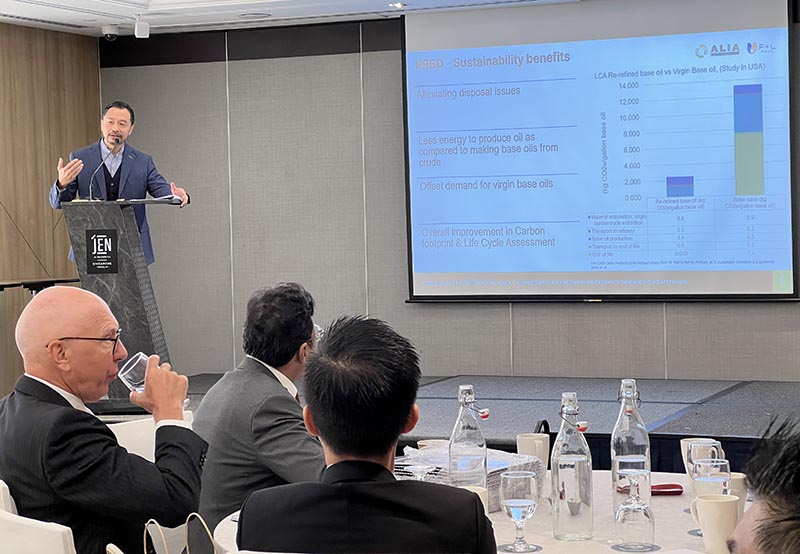
India’s legislation is one of several commitments to drive the adoption of RRBO. The Narendra Modi-led government has established a committee for used oil management and developed RRBO action plans for automotive OEMs and lubricant manufacturers. A draft Mineral and RRBO Specification was published by the Bureau of Indian Standards (BIS) in May 2023, which includes sulfur and saturate content limits and viscosity index criteria. The specification is expected to be updated by early 2024, says Padmanabhan.
Despite apparent efforts to accelerate the adoption of RRBO, multiple concerns were raised during the ALIA Seminar due to the current state of India’s re-refining industry. The ALIA and F&L Asia Ltd co-sanctioned event attracted executives from many of the leading lubricants businesses in Asia.
Gupta emphasised that the penetration of RRBO in India remains “abysmally low,” with only 27,000 tonnes (KT) of RRBO produced. The EPR needs to be revised to a more “modest and achievable target,” he says, with additional policy support focused on regeneration. Of the approximately 1.3 million tonnes of used oil generated annually in India, less than 15% is recycled. Inadequate collection infrastructure, high burn rates, used oil in fuel oil and other distillate products, high feedstock costs and low margins are all contrary to a flourishing RRBO industry. Gupta also highlighted declining demand for Group I base oil, which means RRBO must meet Group II specifications. Majority of India’s virgin base oil consumption has shifted to Group II, according to Padmanabhan.
Gupta also outlined a lack of scale in re-refining infrastructure, with approximately 400 small-scale used oil processing units in operation. To achieve the proposed EPR guidelines, an investment of approximately USD2 billion in both brownfield and greenfield re-refining assets is required, says Gupta. More specifically, 38-40 modern re-refineries, each with a 50 KT feed capacity, are required in a six-year timeframe, he says.
In a presentation on RRBO Legislation: A Perspective on Implications for the Lubricants Industry in India, Paul Nai, director, Product Management, at Lubrizol South East Asia Pte Ltd, stressed that RRBO quality remains a key concern in India. Lubrizol is one of the key lubricant additive suppliers in India.
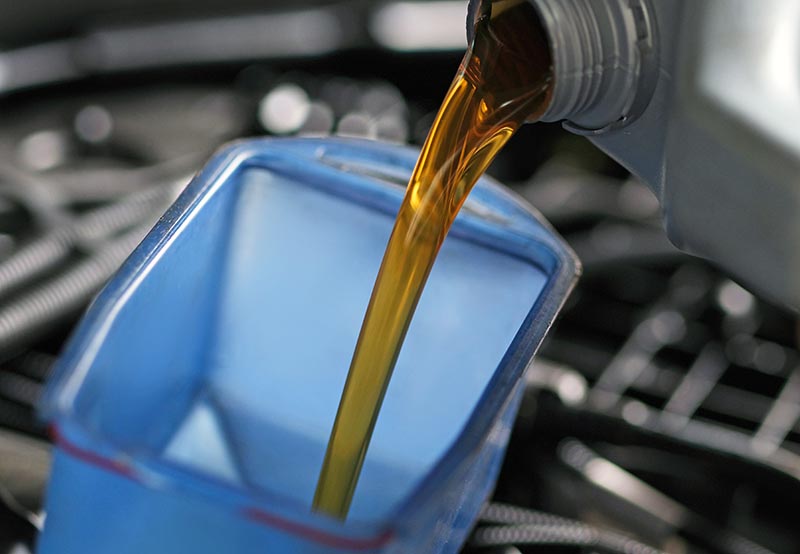
Nai shared the results of a Lubrizol study on SN150 Grade RRBO which evaluated both imported and regional oils. Seven samples from different suppliers displayed broad variances in sulfur content, saturates and viscosity index. Only four of the samples achieved the BIS RRBO specifications for low sulfur which is suitable for automotive applications.
A secondary assessment evaluated multiple samples from the same supplier. Further consistency issues were identified, with Nai detailing conflicting characteristics and base oil group variances. Of six samples, three were classified as Group I, two were Group III and one failed to meet any group criteria, as determined by API 1509, which describes the voluntary API Engine Oil Licensing and Certification System (EOLCS).
Shifts in base oil properties pose multiple challenges for lubricant manufacturers. Base oil interchange guidelines vary for different groups of base oil and alterations in base oil properties can impact API engine oil licensing. Nai also highlighted the effects of inconsistent saturate levels on oxidation performance and drain intervals. Changes in sulfur content can impact after-treatment systems and fuel efficiency, creating additional concerns. A lack of uniformity further complicates the formulation process, particularly when creating fuel economy (FE)-driven viscosity grades such as SAE 0W-16, 0W-20, 5W-30, and 10W-30, he says.
With technology advancements, RRBO quality is generally improving. However, Nai emphasised the challenge of developing universal formulations and the need to test base oils before formulation. To achieve desired vehicle performance standards, robust additive technology is required, and RRBOs need to adhere to qualifying specification limits, says Nai.