Performance Additives for Metalworking Fluids with Regard to Electric Mobility and CLP Ban
Two major challenges for lubricant manufacturers are the transformation of the automotive industry towards electric mobility and the ongoing restrictions of chlorinated paraffins in metalworking fluids.
The broad implementation of electromobility has a significant influence on the kind and complexity of metalworking processes used for car manufacturing and will lead to a replacement of many chip removing metalworking processes by forming or separating operations. Whilst chip removing processes like grinding, milling or drilling are predominantly run by using water-mixed metalworking fluids, forming and separating processes like deep drawing, stamping or fine blanking are commonly using neat metalworking fluids based on oil or solvents. The most important properties of forming and separating fluids are the prevention of cold welding and the reduction of tool wear. Thus, they require balanced combinations of suitable extreme pressure and anti-wear additives.
Chlorinated paraffins (CLP) are still widely used in metalworking fluids for a broad variety of manufacturing processes, particularly for heavy-duty processes like broaching, deep drawing or fine blanking of high strength alloys. Short chain chlorinated paraffins however are already banned from use in metalworking fluid formulations in many regions; medium chain chlorinated paraffins are supposed to follow soon. In most cases it is possible to replace chlorinated paraffins by alternative performance additives. This will not always be an easy 1-to-1 substitution, but by combining suitable lubricant additives it is possible to adjust the characteristics of the metalworking fluids to the specific demands of the metalworking processes and to even exceed the performance of chlorinated paraffin containing cutting and forming lubricants.
The presentation will show which additives and additive combinations can be used to meet the demands of e-mobility related manufacturing processes without using chlorinated paraffins.
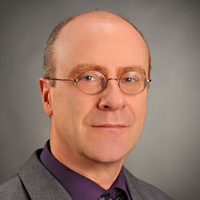