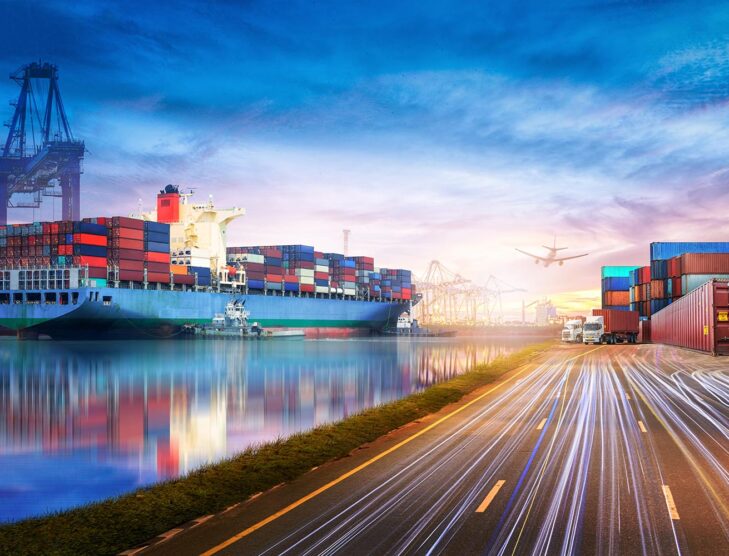
Beyond carbon footprints
As climate change takes centre stage on the global agenda, businesses are realising that measuring and disclosing their carbon emissions is not just an ethical imperative but a strategic necessity. Governments and regulatory bodies are beginning to enact stringent measures, compelling companies to assess, monitor and report their environmental impact.
However, accurately reporting on the carbon footprint of an organisation and its products is easier said than done. During the ALIA Seminar on Sustainability in the Lubricants Supply Chain, held in Singapore on November 6-7, 2023, Chee Kong Chung, managing director of Smart Tradz Pte Ltd, outlined The Practical Way to Jumpstart and Sustain Product Carbon Footprint Reporting and Analysis for the Lubricants Industry.
Smart Tradz is an end-to-end digital and carbon emission management platform powered by artificial intelligence, blockchain, cloud and IoT technologies. The company is headquartered in Singapore, with an office in Malaysia. Chung has more than 25 years of consulting experience in areas such as supply chain management, carbon footprint and decarbonisation across the oil & gas, chemicals, pharmaceuticals, consumer products and electronics industries.
In his presentation, Chung summarised a wide range of “confusing” industry, regulatory and stock exchange greenhouse gas (GHG) reporting requirements, each involving a different level of carbon footprint models and granularity. The Smart Tradz executive also outlined the varying roles of corporate and product-level carbon footprints.
Understanding and managing product-related GHG risks helps companies to ensure long-term success in a competitive business environment and to future proof for regulatory change, says Chung. It also provides an opportunity to capture new business opportunities when segments of the market are prepared to pay a premium for low-carbon products. There is a need for product carbon footprints (PCF) to meet the expectations of customers—increasingly in a B2B environment. Suppliers who do not provide PCFs will limit their ability to continue with contracts, he says.
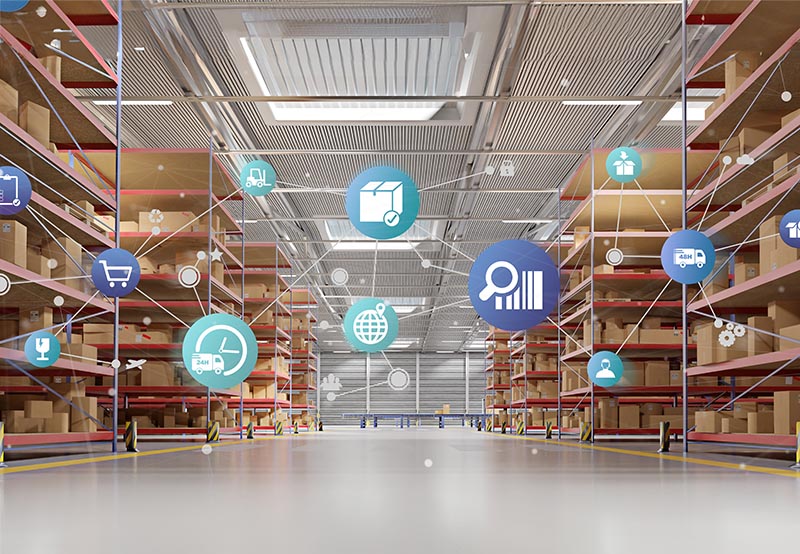
A range of cross-sectoral product lifecycle accounting and reporting standards exist, such as the GHG Protocol and ISO 14067, as well sector-specific rules and product-specific guidelines from organisations such as the Union of European Lubricants Industry (UEIL), the Technical Association of the European Lubricants Industry (ATIEL) and the American Petroleum Institute (API). Chung outlined several limitations in current PCF approaches due to inconsistency in existing methods and standards, which leaves much room for interpretation.
The standard approach to PCFs is to use secondary emissions data in most of the calculations, says Chung. There is growing pressure for the reporting to be done more accurately, with momentum around transferring from secondary to primary data. To do so, we need greater collaboration across the entire ecosystem. A transition towards more accurate primary emissions factor data will help tremendously in delivering more accurate PCF calculations, he says.
Beyond the data, Chung stressed the importance of harmonisation of methodology. If there is no coordination in terms of how calculations are done, this will impede companies from drawing the appropriate conclusions, he says. An appropriate framework will enable the granularity of data required for accurate calculations. Using aggregate data or averages is very commonplace right now, says Chung, and there is a need for more granular level transaction data to ensure more exact carbon numbers.
Reporting carbon footprints for stock exchanges, regulatory measures and PCFs require different levels of data. However, companies need to avoid the “nightmare” of employing different tools for different reporting requirements, says Chung. A system that can handle all aspects, including PCFs, is critical, he says.
The “big ticket” items in PCF calculations are raw materials and end-of-life. Packaging can also be a significant contributor. Transportation is one area that is often overlooked in PCFs, says Chung. Oftentimes, the reason given is that transport emissions are not that large, proportionally speaking.
However, transportation emissions often take an aggregate approach—and can be grossly inaccurate, says Chung. If you don’t have a granular view, it is impossible to understand the impacts of different transportation modes and providers, and easy to miss opportunities to significantly reduce the carbon impacts of transportation.
In the lubricants industry, carbon measurement is relatively immature—and is still battling with cradle-to-gate numbers. If companies are serious about moving to the more precise cradle-to-grave approach, there are “still a lot of issues in terms of data transparency,” says Chung. A greater understanding of material flow is required with improvements in the traceability of materials from origin to destination.
Chung highlighted the example of a battery passport developed in the electric vehicle industry. On January 18, 2023, the Global Battery Alliance (GBA) officially launched the world’s first battery passport proof-of-concept at the Annual Meeting of the World Economic Forum in Davos, Switzerland. The battery passport aims to deliver a trusted carbon footprint and greater transparency along the entire battery value chain.
The passport is essentially a digital twin of the physical battery that conveys information to all stakeholders about the product carbon footprint along the value chain, tracing all the way to upstream emission sources such as carbon intensity from the mining and refining sector for the metal materials used in electric vehicle (EV) battery production.
A “digital twin” is a virtual model designed to accurately reflect a physical object, system, or process. This concept is widely used in various industries, including manufacturing, automotive, healthcare, and urban planning. While such an approach is not currently available in the lubricants industry, Chung believes it is a trend that will one day reach the sector.
The Smart Tradz executive also outlined the company’s efforts to collaborate with universities to advance its carbon measurement technology. A value chain “Collaboration Hub” uses blockchain technology to improve the visibility of material flow, tracking molecules and ensuring data collected along the value chain is tamper-proof. Such Value Chain Collaboration Hub also enables emission factor data sharing among supply chain ecosystem partners such as between suppliers and customers, to support a more accurate Scope 3 emission measurement for both corporate and product carbon footprint. Eventually, the lubricant industry will benefit from this kind of transparency and trustworthiness, he says.
During the ALIA Seminar’s panel discussion on Product and Process Aspects of Sustainability, Karen Lee, business vice president of Process Automation Business at Schneider Electric, described efforts by the lubricant supply chain to improve data traceability and data integrity. Schneider Electric is working with the top 1,000 suppliers, responsible for 70% of upstream emissions, on decarbonising operations.
The first step is to collect data as efficiently as possible—without human intervention—such as using sensors and eliminating manual entry into spreadsheets. Consolidation of data is another challenge when trying to avoid manual data entry. Lee noted several key gaps in data collection at manufacturing sites. Many facilities do not have a “historian”—responsible for the storage of archive operational data, which is typically time-stamped to ensure data robustness.
A key focus of the ALIA Seminar was recent legislation in India mandating the use of re-refined base oil (RRBO) in all finished lubricants sold in India by April 2024. The RRBO component increases annually throughout the decade. There are uncertainties around how to incorporate RRBO into PCF calculations, says Chung, particularly in instances where RRBO is not continuously fed to the operation. However, from a methodology perspective, recycling calculation methods such as cut off/recycled content are well established.
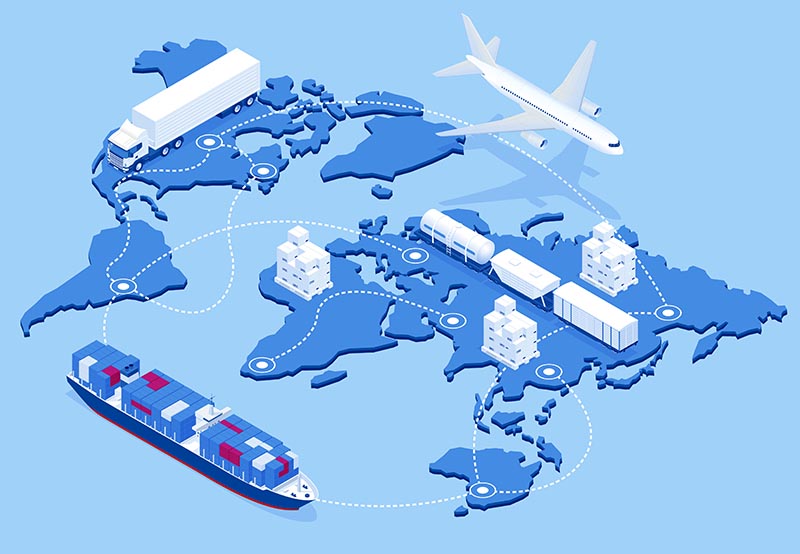
The lubricants industry continues to grapple with Scope III emissions, says Chung. Methodology is well established for Scope III, such as the GHG Protocol. However, the GHG Protocol does not have the requisite level of detail in some areas when it comes to practical implementation, says Chung. For example, it does not outline how to handle transportation in a detailed manner. Even the Global Logistics Emissions Council (GLEC) Framework, a globally recognised methodology for calculating and reporting the greenhouse gas emissions from logistics operations, does not tell you how to model door-to-door, he says. To make Scope III practical, real-world methodologies need to be incorporated, that include domain knowledge, supply chain and procurement.
The lubricants industry continues to grapple with Scope III emissions, says Chung. Methodology is well established for Scope III, such as the GHG Protocol. However, the GHG Protocol does not have the requisite level of detail in some areas when it comes to practical implementation, says Chung. For example, it does not outline how to handle transportation in a detailed manner. Even the Global Logistics Emissions Council (GLEC) Framework, a globally recognised methodology for calculating and reporting the greenhouse gas emissions from logistics operations, does not tell you how to model door-to-door, he says. To make Scope III practical, real-world methodologies need to be incorporated, that include domain knowledge, supply chain and procurement.