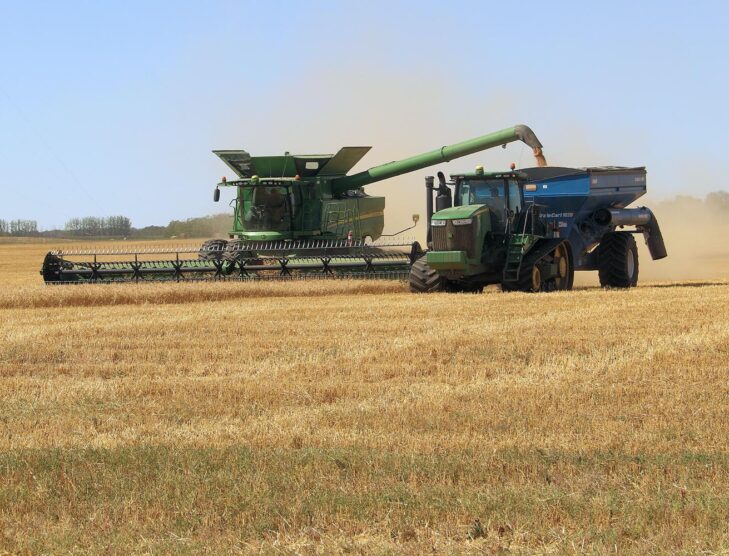
Electrification is about controllability, not sustainability
Mobile working machines (MWM) describe a wide range of vehicles or equipment designed to perform specific tasks or operations while in motion. Typically, they undertake dedicated work while driving or at various locations and they consume significant energy. MWMs are commonly used in the agriculture, forestry, construction and logistics sectors and may include machines such as tractors, cranes, excavators, combine harvesters, bulldozers, drone technology and other specialised equipment.
MWMs are exposed to harsh operating conditions. A historical trend toward bigger machines has been evident as demands on the performance of MWMs continued to grow. As companies look to maximise productivity and optimise energy efficiency, this decades-long trend is set to reverse in some areas, says Nicolas Huber, staff engineer at John Deere Corporate Materials Engineering, Lubricants.

Huber has worked at John Deere since 2001, a company renowned as a world leader in the manufacture of agricultural equipment. John Deere also produces products and solutions for the construction and forestry industries, drivetrain solutions and heavy-duty diesel engines, as well as additional solutions and services through affiliated companies.
During the 1st International Conference on Tribology and Sustainable Lubrication, held in Düsseldorf, Germany, on April 18-19, 2023, Huber delivered a presentation on Lubrication for Next Generation Mobile Working Machines where he emphasised that the future of MWMs will be electric.
A move away from fossil fuels is already evident in the transportation, equipment and material sectors as companies look to lower emissions and improve air quality. However, a push to electrification of MWMs is not about sustainability, it is about controllability, says Huber.
Next-level productivity requires precision, speed and autonomy, and this demands enhanced controllability. Machine controllability is the enabler for next-generation productive and efficient machine solutions. Doing this the right way, the result is sustainable, he says.
The next generation of MWMs will feature different e-concepts, working conditions, life cycles and levels of system functionality, says Huber. His presentation focused on three electric system architectures including a generated electric system (GEL) where the internal combustion engine drives a generator that produces the electricity to propel electric motors. GEL allows enhanced productivity and improved efficiency. Precision placement of seed, fertiliser and chemicals are potential benefits of employing this system.
A conventional battery electric system (BEL) is appropriate for low- to mid-power applications in an urban environment. BEL features zero emissions, quiet operation, ease of use and reliability. Lastly, a hybrid electric system enables higher productivity, idle avoidance and engine downsizing.
Huber highlighted the influence of labour shortages, price pressures, and a need for rationalisation and efficiency on machine topology—encouraging more evolved designs. There is a pressing need to improve today’s machines by tailoring them to more specific tasks or applications, he says.
However, the John Deere representative insists that future MWM designs will incorporate the same three electric systems arranged in different architectures. Larger, more complex equipment may have a mix of solutions or even all three in a single system, he says. It should be noted that fuel cells were outside the scope of Huber’s presentation.
With complex machines come more complex lubricant requirements. The need for different fluid solutions can be traced to different working conditions between on- and off-road applications. While on-highway vehicles are subjected to relatively low loads and low energy consumption in a clean environment with a narrow application range, off-highway MWMs not only drive, they work. MWMs and their lubricants can be exposed to high loads—up to 95% power use 90% of the time, higher energy consumption, minimal airflow, dusty, wet and cold conditions—as well as agricultural chemical contact. Off-level operation, often associated with strong vibrations and shock loading, is also a challenge.
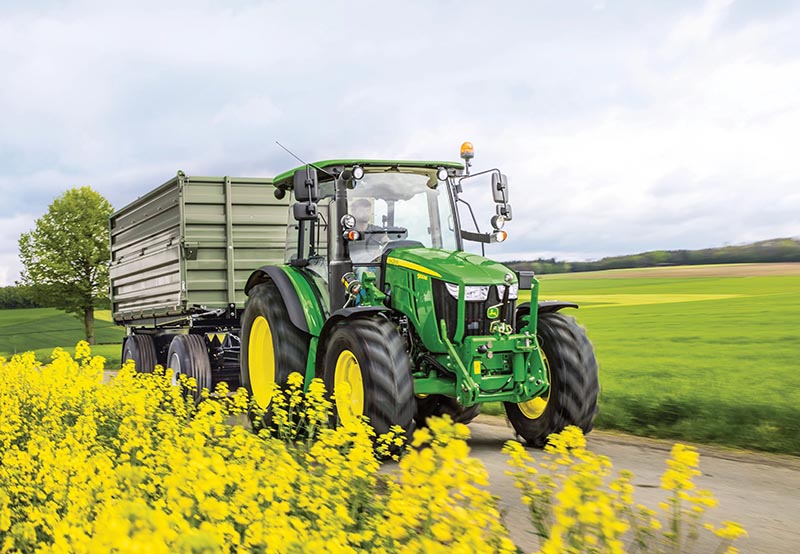
One of the most important demands of MWMs is low downtime. Huber emphasised that reliability requirements differ significantly from on-road applications—in particular, light-duty vehicles. For instance, electric cars may have a reliability goal of 100,000 miles with a continuous power requirement of less than 10 kilowatts (kW), whereas a tractor’s reliability goal can reach 1,000,000 miles (equivalent) with continuous power greater than 100 kW. Fluids for current electric drivelines are not sufficient to service future customer needs in electric MWMs, he says.
A trend to autonomy is evident in mobile working machines—not only for convenience but also safety, efficiency and to counter labour shortages. Electrification and autonomy will change the way MWMs will look and operate, says Huber. The new John Deere 8R tractor with fully autonomous operation will go into “serious production” at the end of this year, he says.
Greater autonomy will likely result in more specialised, less versatile fluids, says Huber. Without an operator, fully autonomous machines lose their main sensor. Machine condition monitoring and machine health detection need to be brought to the next level and need to actively involve the lubricant. This is something that requires more industry focus, he says.
The absence of an operator and electrification will spark a new era for machine layouts. Electrification will change the arrangement of components and this new machine topology will impact lubrication. The strict need for orientation on a driveline and rotating shafts is repealed. Drives will be located where they are needed. Huber expects increased grease usage in the future in such machines, particularly in auxiliary drives mounted in remote locations. Huber also anticipates a greater number of independent fluid sumps.
The combustion engine is the major driver of recurrent service events. The advancement of electrified autonomous machines will also result in longer service intervals including increased fill-for-life, says Huber.
A reversal of the historic trend to bigger machines is inspired by greater autonomy. Huber signposted an increase in the number of simple, less versatile units with a continuing increase in power density and heat.
Manufacturers will need to completely redefine their approach to cooling modern mobile working machines. For example, applications powered by hydraulics currently get cooling and lubrication “for free.” Electrification of these applications means you must suddenly start taking care of cooling and lubricants, says Huber.