
Smart factories: Rise of the machines
You might associate the phrase “rise of the machines” with highly advanced, malevolent robots from some science fiction movie starring actor and former bodybuilder Arnold Schwarzenegger. However, as demand for consumer goods continues to swell and competition in manufacturing becomes ever more intense, companies are turning to machine automation to continue to survive and thrive.
The desire to enhance the performance of an organisation and to circumvent rising costs such as wages, benefit packages, education and training, health and safety compensation is encouraging the development of smart factories and the use of cost-effective and energy-efficient robots.
A high initial cost can be a roadblock to the adoption of robotics. Though, the average selling price for a robot has declined by more than half in the past three decades, increasing adoption in multiple industries. Data from the International Federation of Robotics (IFR) observed an 85% increase in global operational stocks of robots in the five years to 2020. The automotive industry is one of the most critical applications of industrial robots.

Robots can be programmed to carry out autonomous tasks or support manual processes. They can replicate human actions and perform routine chores or more dangerous activities. Benefits to a manufacturer can include a productivity boost, declining labour costs, heightened worker safety, greater levels of precision and a cleaner working environment with a lower risk of contamination. The technology can also support a lower cost of reshoring manufacturing.
Previous research has found that a recessionary environment accelerates automation as humans become comparatively more expensive due to a drop in company revenues. The onset of Covid-19 may have resulted in a brief pause in robotics growth as companies dealt with pressing issues such as nationwide or regional lockdown. Nevertheless, analysts are anticipating a Covid-19-induced surge in the robotics market in the upcoming years as companies and industries substitute humans for robots to mitigate the impact of the virus, overcome supply chain shortages and counter the impacts of an ageing workforce and the current labour shortage. For companies that may have been reticent, Covid-19 could be the catalyst for change.
The fourth industrial revolution, dubbed “Industry 4.0”, refers to the trend of automation and data exchange in manufacturing technologies. As smart factories become more prevalent, the size of the robotics market is set to increase. Though, growth projections vary markedly. A report on How robots change the world by Oxford Economics estimates robots will multiply rapidly to 20 million units by 2030. The Boston Consulting Group (BCG) expects the robotics market will reach USD87 billion by 2025, in what some have called a conservative assessment. Several analysts have predicted double-digit annual sales growth in the sector. Asia Pacific is likely to lead the way with growing automation in Japan, China and India. While Japan is dogged with an ageing population and a declining birth rate, China and India are the most populous countries in the world.
Factory automation does not come without its challenges. A widely quoted survey of auto industry manufacturing executives suggests a solitary minute of downtime can cost an automotive manufacturer around USD22,000. To get the most from your cybernetic workforce, robot maintenance is critical. In particular, choosing the correct lubricant is vital to keeping robots running efficiently.
Industrial operations often use articulated robots featuring six axes, presenting a high degree of flexibility and the capacity to undertake a wide variety of tasks. Robots require lubrication on any joint that moves, whether actuated joints, bearings, sliders, chains, or in gearboxes. Demand for high-quality lubricants is expected to rise alongside robotics market growth.
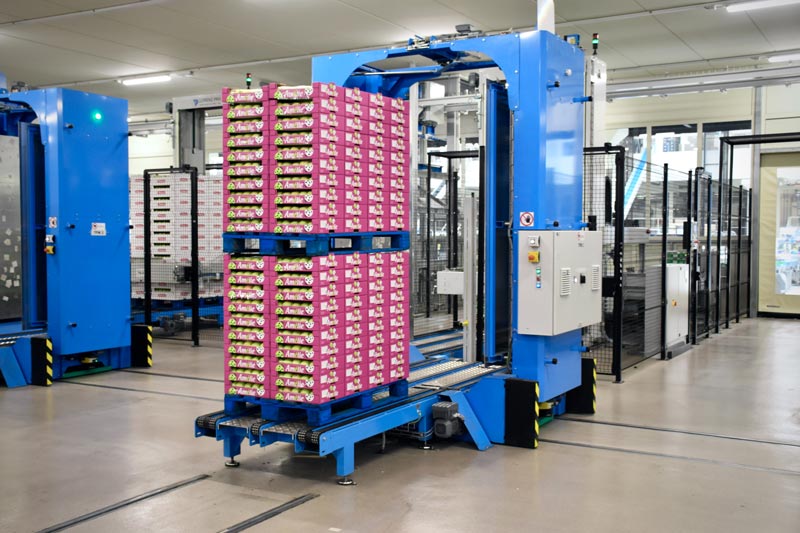
A recent white paper by Castrol, bp’s lubricant brand, entitled Robotics on the Rise: Fueling the Factory of the Future noted that one leading automotive OEM was spending more than 60% of its lubricant budget on robotics. The white paper was based on qualitative research examining the challenges of servicing and maintaining robots in industrial manufacturing. More than 25 robot and aftermarket OEMs from the automotive and electronics sectors in the U.S., Europe, China and Japan were involved in the study.
Castrol’s white paper highlighted three key challenges associated with lubricant selection in robotics—reliability, efficiency and convenience. On reliability, OEMs identified protection against leakage as their number one concern. The need to avoid contamination in a cleanroom or prevent waste and expensive product leaks into the body of a car were cited as examples. Robotic lubricants must also reliably withstand temperature extremes. Low temperatures can congeal lubricants, triggering over-torque or collision alarms. The importance of anti-wear was also outlined.
The role of lubricants in increasing production efficiency, production yield, and maintenance efficiency was emphasised in the white paper. However, the research indicated that environmental concerns were becoming top of mind and energy conservation is a high priority. Reductions in friction allow robots to operate at lower temperatures, which reduces energy usage and environmental impact.
Survey participants highlighted an opportunity to increase the accuracy of robots and reduce waste using advanced lubricants. Precision checking and lubrication are time-consuming aspects of robot maintenance, according to OEMs. The research underlined the need for a convenient, simple-to-use lubricant that is long-lasting and brand agnostic, to ensure the maintenance process is as straightforward as possible.
Effective automation relies on excellent lubrication; however, the report identified several barriers to switching lubricant products, including a lack of knowledge and technical expertise as well as general concerns relating to the durability of lubricating oil versus grease.
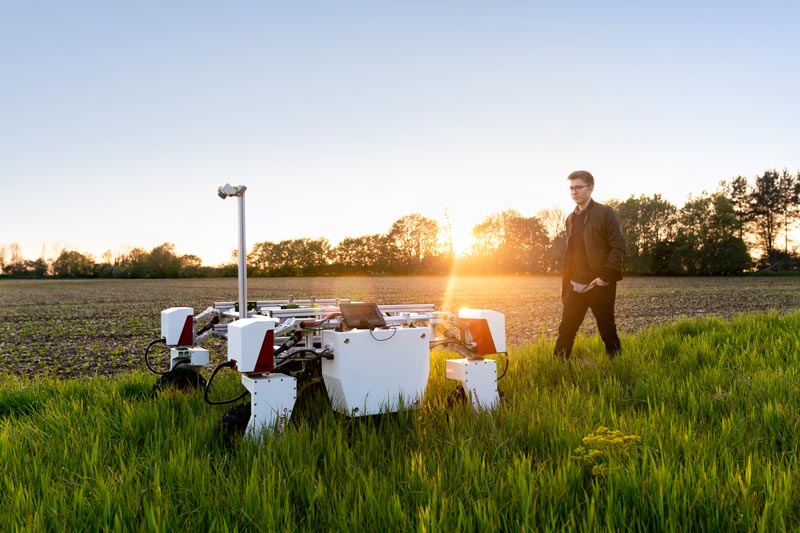
Castrol’s Rise of the robots underscored the importance of product development and innovation in overcoming the challenges of robot maintenance and ensuring solutions are aligned with evolving robot designs. The researchers identified a need for a fully synthetic formula that provides improved oxidation stability—to enable a service interval goal of 20,000 hours. Advanced lubricants that reduce carbon emissions and environmental impact during manufacturing, such as those with bio-sourced raw materials and re-refined base oils, were also highlighted.
A balancing act exists between higher use of additives to protect against wear, like plastic deformation additives that can minimise friction within robots, and the resultant residue which prevents the lubrication of sealing systems and can lead to leakage. The next generation of robotics lubricants must have optimised additive levels to extend robot lifetimes while eliminating leakage, says Castrol.
Developing appropriate products to support the transition to robotics is important; however, the Castrol study revealed that aftermarket customers are also looking for suppliers that can add value. Customers require education and training on solutions that are available and, to get the most out of their robots, end-users need more information. Most end-users currently lack the requisite level of knowledge when it comes to best maintenance practices, says Castrol.
The primary area of focus for education is around the capabilities of oil versus grease, such as durability and reliability under extreme temperature conditions. Castrol also noted the importance of educating consumers that the cheapest lubricant isn’t necessarily the best option due to a trade-off in performance.
While technology is likely to play a major role in robotics lubrication and simplifying maintenance moving forward, the Castrol paper indicated there is a long way to go before it makes end-users’ lives easier. Lubrication maintenance software is still in its infancy, leaving many customers to base maintenance decisions on experience over data, relying on well-trained and senior in-house maintenance teams.
The biggest technology opportunity is in improving maintenance intervals, says Castrol. The report highlights the potential for used oil analysis to aid in widening the service intervals of robots by completing oil checks on the hardest working machines. The value of data analytics in the maintenance of robots—specifically condition monitoring and smart lubrication— must be weighed against set-up and operational costs, says Castrol.