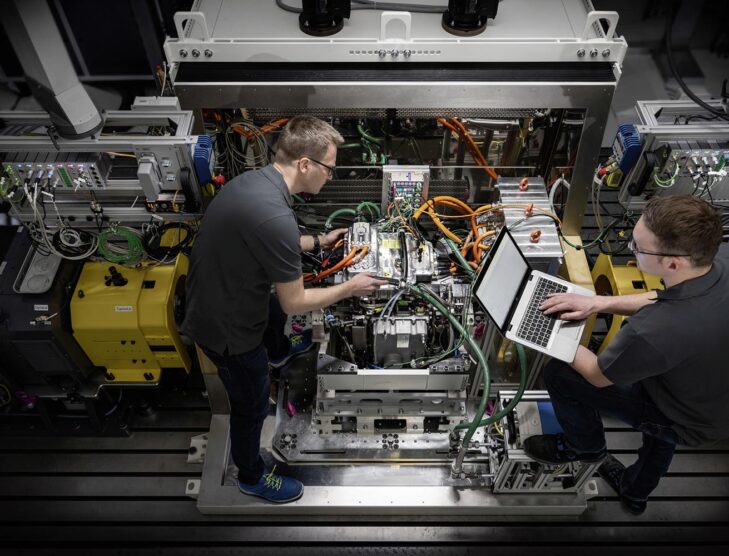
In the future, e-Axles could become staple of electric powertrains
Competition is heating up in the electric vehicle (EV) arena as traditional automotive manufacturers expand their vehicle range to contend with the emergence of all-electric start-ups. Keeping up with the rapid rate of change requires manufacturers to operate with speed and agility.
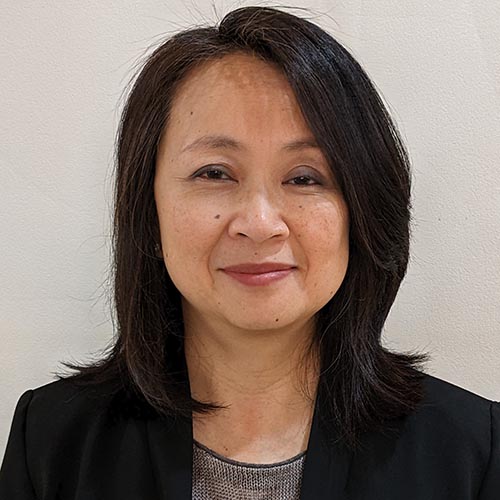
An e-Axle is a modular drive unit that combines several elements of electric drive technology into one simple package. Typically, an e-Axle includes an electric motor and reduction gear set (transmission) and it can also contain power electronics in one compact unit. The all-in-one solution requires less space than the sum of its parts and fits easily into existing vehicle architectures, reduces complexity and is more cost-effective to manufacture due to the lower number of components. Importantly, e-Axles can shorten development timeframes and provide a simple, scalable option.
Demand is expected to rise alongside a trend towards higher integration of hardware components, with many believing e-Axles will become a staple of electric powertrains. The solution can apply equally to passenger cars, commercial and heavy-duty vehicles. Some analysts have forecast compound annual growth rates (CAGR) of more than 30% in the coming years.
In terms of mass production of vehicles which use e-Axles, China is leading, says Dairene Uy, project lead for transmission fluids at Shell Global Solutions (US) Inc. She is based at the Shell Technology Center in Houston, Texas, U.S.A. Although, the Shell representative notes, higher technical innovation and engineering complexity come from premium OEMs, mostly located in Europe, the United States or Japan. With e-Axles yet to reach technical maturity, OEMs are still wrangling whether to develop in-house capabilities or work closely with Tier 1 suppliers to differentiate technology from their competitors.
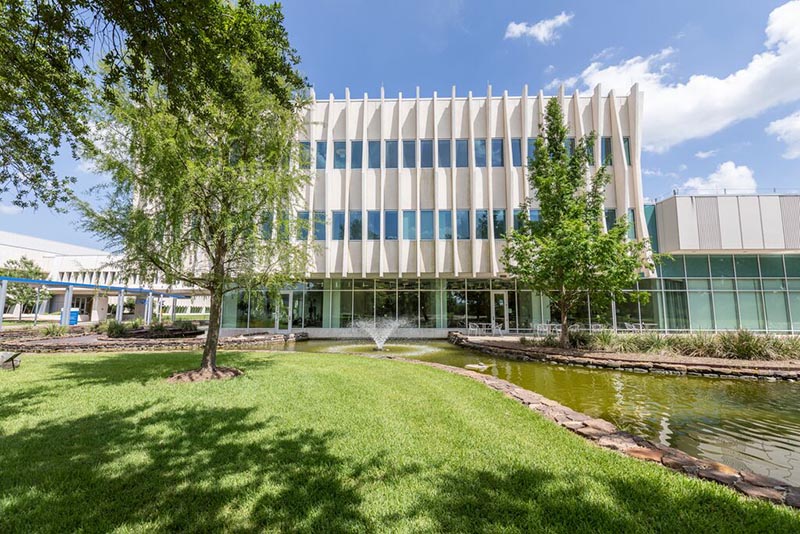
Suppliers such as Bosch, GKN and Magna have already developed e-Axle solutions to satisfy growing demand and on September 27, 2022, Hitachi Astemo announced it had received e-Axle orders for mid-size and large-size battery electric vehicles (BEV) from Honda Motor Co., Ltd, for a global rollout in 2026. A proliferation of e-Axle hardware designs exist. With greater production volumes, further standardisation of architecture makes economic sense.
EVs are already associated with lower maintenance in comparison to a typical petrol or diesel car. Gone are the days of oil changes, fuel injector replacements and cleaning of diesel particulate filters. e-Axles themselves are designed to be almost maintenance-free. So, can we say goodbye to ongoing vehicle maintenance?
With fewer moving mechanical parts, we can reasonably expect reduced maintenance requirements from an e-Axle compared to a traditional powertrain. โStandard maintenance would be defined differently,โ says Uy. The market is new and still evolving and a variety of hardware designs and configurations exist. Standard maintenance would vary from a passenger car to commercial vehicles in different classes or different usage profiles, she says.
Shell expects a type of aftermarket to open up for passenger and commercial vehicles that might be similar to maintenance intervals for conventional vehicles. We would expect high voltage safety requirements to be part of standard maintenance, says Uy.
There are additional challenges in the maintenance and repair of e-Axles, with access to components inside the unit becoming more difficult. In terms of repair, there have been suggestions that in the future units could be exchanged or swapped out at a typical workshop in the case of failure, with specialist repairers required for e-Axle repairs.
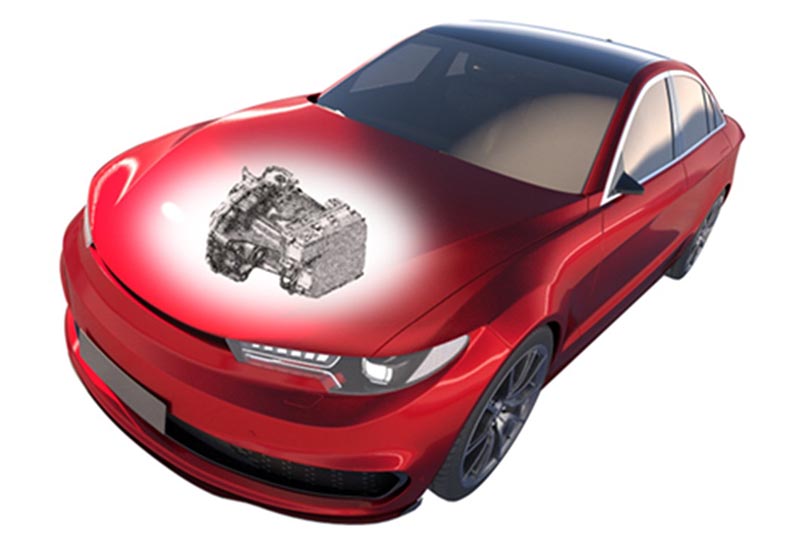
The higher the demands on a lubricant, the more likely a dedicated fluid will be required. Currently, e-Axles can use conventional ATF or gear oils depending on usage or configuration, although there are OEMs that are using specialised e-Axle fluids. Shell launched its Shell e-fluids portfolio in 2019, which was extended to commercial vehicles the following year.
Integration of the electric motor, axle systems and power electronics extends the lubrication requirements beyond traditional transmission fluids. However, โit is no different from the conventional transmission and driveline world where lubricants are developed according to OEM specifications and requirements,โ says Uy, who was formerly with Ford Motor Company in Dearborn, Michigan, U.S.A. Groups are being formed to better understand the needs and test requirements of new e-fluid technologies in this nascent sector.
In general, lubricant requirements are defined based on whether the motor is being lubricated and cooled by the transmission/axle lubricant, says Uy. If the motor is dry, then a conventional lubricant can be used. If the motor is integrated into the e-Axle and cooled by the same fluid, the requirements are more stringent, she says.
Compatibility with electrical components is critical for wet e-motors. This requires the development of new additive systems that balance conventional properties like wear protection and compatibility with components such as insulating materials, seals and copper windings, says Uy. Antiwear and extreme pressure additives must be blended carefully to still deliver compatibility with critical electrical properties, and enhanced friction performance and other lubricant attributes must not be allowed to adversely affect e-Axle materials.

Additive systems for e-Axles contain much less sulphur than those of conventional axle fluids. The Shell representative emphasised the need to introduce alternative wear protective additive systems without sulphur, which can form deposits with copper.
Uy identified several technical challenges in lubricant formulation for e-Axles including thermal needs, foaming due to high-speed motors, electrical resistivity and material compatibility requirements for lubricants that have contact with the electric motor. Any future moves to require wet e-Axle lubricants for heavy-duty vehicles to meet API GL-5 or SAE J2360 standards would also prove a significant challenge, says Uy. API GL-5 is typically recommended for hypoid gears in automotive axles operating under high-speed, high-load conditions. SAE J2360 covers multipurpose gear lubricating military oils and encompasses and exceeds API GL-5.
The integration of an electric motor in electric drive units allows for the efficient design of a single cooling circuit, but this places additional demands on the lubrication system. There is an increasing use of low-viscosity fluids in e-Axles to deliver greater efficiency and improve heat transfer properties. Although, โcooling requirements are not always as high as expected,โ says Uy. Some e-Axle designs are delivering lower fluid temperatures than in conventional driveline applications. Additives need to be adjusted to work in these scenarios, she says. Shell expects the trend towards lower viscosity fluids to continue alongside increasing focus on cooling properties.
There are many new entrants and voices in this exciting new field. How the fluids market will play out depends on who the players are. If this follows the conventional transmission and driveline market, there will be a proliferation of hardware designs and fluid requirements with each automotive OEM and Tier 1 supplier providing their own specifications, says Uy.