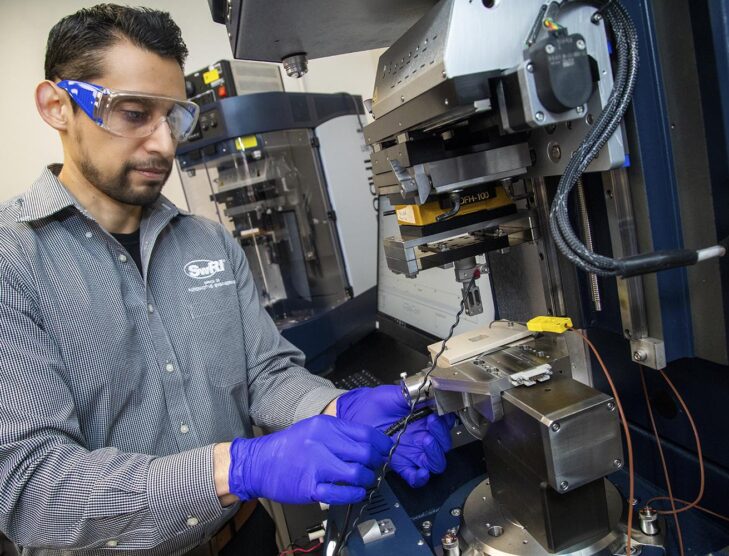
SwRI develops tribology testing device to analyze EV fluids
A Southwest Research Institute (SwRI) in San Antonio, Texas, U.S.A. said it has developed a mechanical testing device to analyze fluids and lubricants specially formulated for electric vehicles (EVs). A team from SwRI has modified a commercial tribology testing device to give it the capability to evaluate the impact of electric currents in fluids, measuring the wear and friction on the automobile parts in the presence of an applied voltage.
“The electrification of the automotive industry has accelerated over recent years, with future projections showing an exponential growth in market share for both light and heavy-duty applications,” said Cole T. Frazier, research engineer with SwRI’s Advanced Drivetrain Lubricants Section. “Traditional fluid testing tools, however, were not developed to effectively analyze lubricant properties in electrified environments. That extends to tribology testing as well.”
Tribology is the study of friction, lubrication, and wear. The challenge for evaluating behavior in EVs is the presence of an applied electrical potential at component and lubricant interfaces. To meet this challenge, Dr. Carlos Sanchez, a senior research engineer in the Tribology Research and Evaluations section, designed a new test apparatus to model the effects of electrification on rotating parts. This small-scale bench test was built around a traditional universal testing machine. The setup and test protocol were further developed by the team throughout the project.
The multidisciplinary team included Frazier, Sanchez, Nolan Erickson (electrical engineer), Dr. Peter Lee (institute engineer), Andrew Velasquez (engineer) and Travis Kostan (senior research analyst).
Most EVs use alternating current (AC) induction or permanent magnet motors, which are powered by onboard battery packs. An inverter takes the direct current (DC) voltage input from the batteries and converts it to the AC power required to operate the vehicle’s motor.
“The numerous rotating surfaces within EVs are exposed to voltage spikes during the DC-to-AC conversion process,” said Sanchez. “The spikes and the inherent electric field in high-voltage environments can allow electric currents to flow through the surfaces, damaging the lubricants and materials that keep them moving smoothly.”
According to the researchers, the speed of the DC-to-AC frequency conversion can cause local voltage spikes that require grounding. Motor bearings are often especially susceptible to electric currents flowing through them due to their location near the voltage spikes. The electric potential for the bearings can build until the voltage becomes strong enough to break down the thin film of lubricant separating the small metal ball bearings from the bearing raceways or bearing shells, which can cause surface damage and scarring.
The team developed and analyzed a test protocol for the new instrument that would best represent the actual system and produce relevant results. Using this new internally funded advancement, they tested several different commercial lubricants and measured wear scarring and friction on the bearing raceways and bearing shells. They found that electric potential across a fluid, whether the current is AC or DC, can affect wear and bearing friction by as much as 20%.
“SwRI specializes in creating custom tribology rigs and testing capabilities to allow the industry to test multiple lubricant formulations efficiently, without requiring full-scale testing,” said Lee, who leads SwRI’s tribology activities. “In this case, because lubricant breakdown is shown to be fluid-dependent, formulators can optimise their lubricants for specific EV drivetrains. SwRI’s bench-scale testing capabilities will accelerate lubricant optimization, improving durability and increasing vehicle range through reduced friction.”